Why Metal Facades
There are lots of reasons to choose metal as a cladding material; it’s durable, beautiful, and recyclable. The range of options with metal cladding is much larger than many other materials because each variable has its own range of additional considerations. Depending on the alloy you select, the appearance, the shape, and the installation method specified, the cost of metal facades range from very low to very high. Let’s look at a few options for designing metal facades which are cost-effective (smaller, thinner, and easier) while still providing all the benefits of metal siding.
Cost is relative. These tips may not get you the least expensive option in every market, but they might be the secret backdoor to getting the right material for your project within budget.
What to watch out for
Installation, movement, and substrates:
Metal moves, a lot. It expands and contracts with changes in temperature more than most building materials, requiring that installations accommodate movement in the clips, folds, seams, and slotted connections used to attach the metal. Another key way to save money with metal cladding systems is by avoiding a complicated substructure. To really take advantage of the characteristics of metal, make sure to detail the facade to allow access to all the parts which might need maintenance, replacement, or repair.
Metal shingles manage movement as a system, distributing the expansion and contraction over many smaller joints rather than stress in the material itself or fewer larger joints. That distribution of stress means that the material can be thinner and still perform. The small, modular nature of shingles can hide oil-canning, small dents, and other imperfections. This also lets you specify a thinner material, which performs well and looks good in small formats, but would not be acceptable in larger formats. The folding of the shingles creates an airspace behind every shingle without the addition of furring, which allows them to be reliably installed directly to a solid substrate such as plywood (with a proper WRB and detailing)
Because of the labor involved in installing shingles, they may not be the most cost-effective option overall, but they are often the most cost effective way to get materials such as copper or zinc which can last for 60 to 100 years saving over the life of the building.
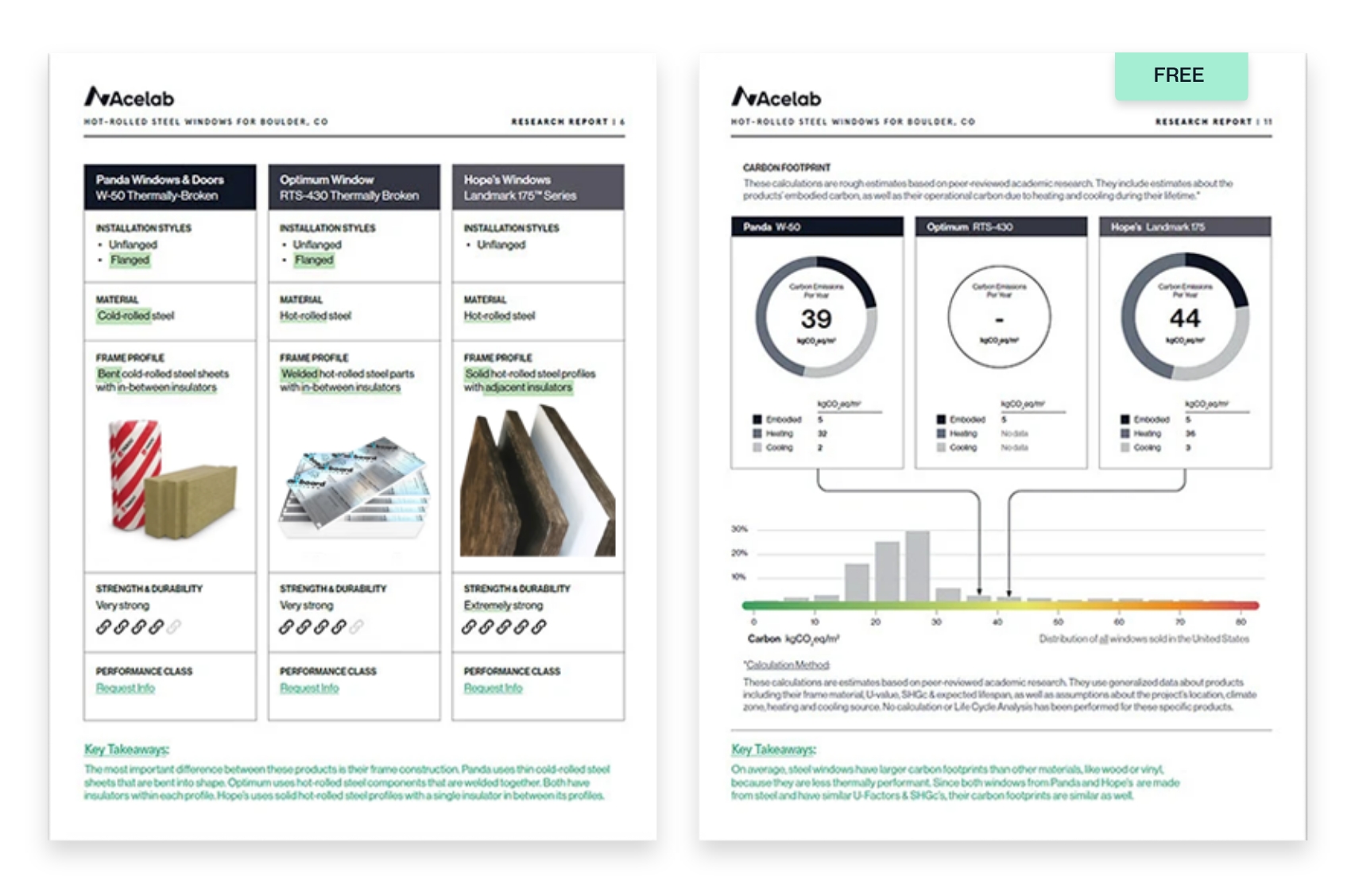
Looking for Metal Siding for your Next Project?
Acelab's advanced search can help you find & compare building products for any project. Learn More
Corrugated metal accommodates movement in the profile of the metal itself, and the smooth curves of sine wave panels do that particularly well. As a less expensive alternative to all those clips, you can directly attach a sine wave panel to just about any solid substrate with screws right through the panel and have a reliable installation. Additionally, the metal only comes in contact with the WRB on the wall at the valley of each curve, creating an effective airspace.
Standing seam panels are primarily anchored to the roof with clips, which are attached to the roof and then covered by the roof panels. The standing seams are carefully folded over each other and the clips to lock them in place. Snap seam systems follow the same basic logic, except they snap onto the clips and each other using profiles engineered and folded in the factory. Depending on the wind load the building will experience, engineered snap lock seams can provide all of the same benefits - and a cleaner, faster installation - with just a little less wind and wind-driven rain performance. On walls (and pitched roofs over 4/12) you're unlikely to run into the design pressures which warrant a mechanically folded seam, and can take advantage of the cost savings of a snap seam system.
Water, rust, and venting:
The most common way metal fails is rusting from the back, and the purpose of all that fussy furring is to keep the metal dry. Water gets behind the metal through tiny leaks at joints, or as vapor which condenses on the back of the metal and needs a way to dry out. Metal is vapor-impermeable - so either the wall has to dry to the inside, which isn't always appropriate, or it needs to vent. Direct attached panels, such as the corrugated panels, or shingles vent at the joints. Standing seam panels need to vent at the top and bottom of the wall.
Copper, zinc, and aluminum don't rust of course, and steel can be protected with a high quality paint or similar coating but even the cost effective, direct attached systems must allow for the wall behind the metal to vent to dry.
Historically, architects used metals and alloys such as copper, zinc, tin, lead, tern, and lead-coated copper, so they didn't have to worry about rust. Today, modern coatings allow steel to last nearly as long (or just as long) with proper maintenance. These tips can make more expensive metals as cost-effective as possible, but steel will almost always have an even less expensive first cost.
Metal walls and roofs are often the same products.
Metal wall systems are an extension of metal roof systems and often the same exact product. While there are different details between walls and roofs, the fundamentals are the same. Not only do these simple systems work on both walls and roofs allowing for elegantly simple composItional projects, but when you're searching for metal walls, search roofs too - the products will probably work.
Traditionally, metal was used for roofs long before it showed up on walls. It keeps water out, lasts a long time, and it’s easily maintained and repaired. As metal has become more common on walls, these same properties are true.
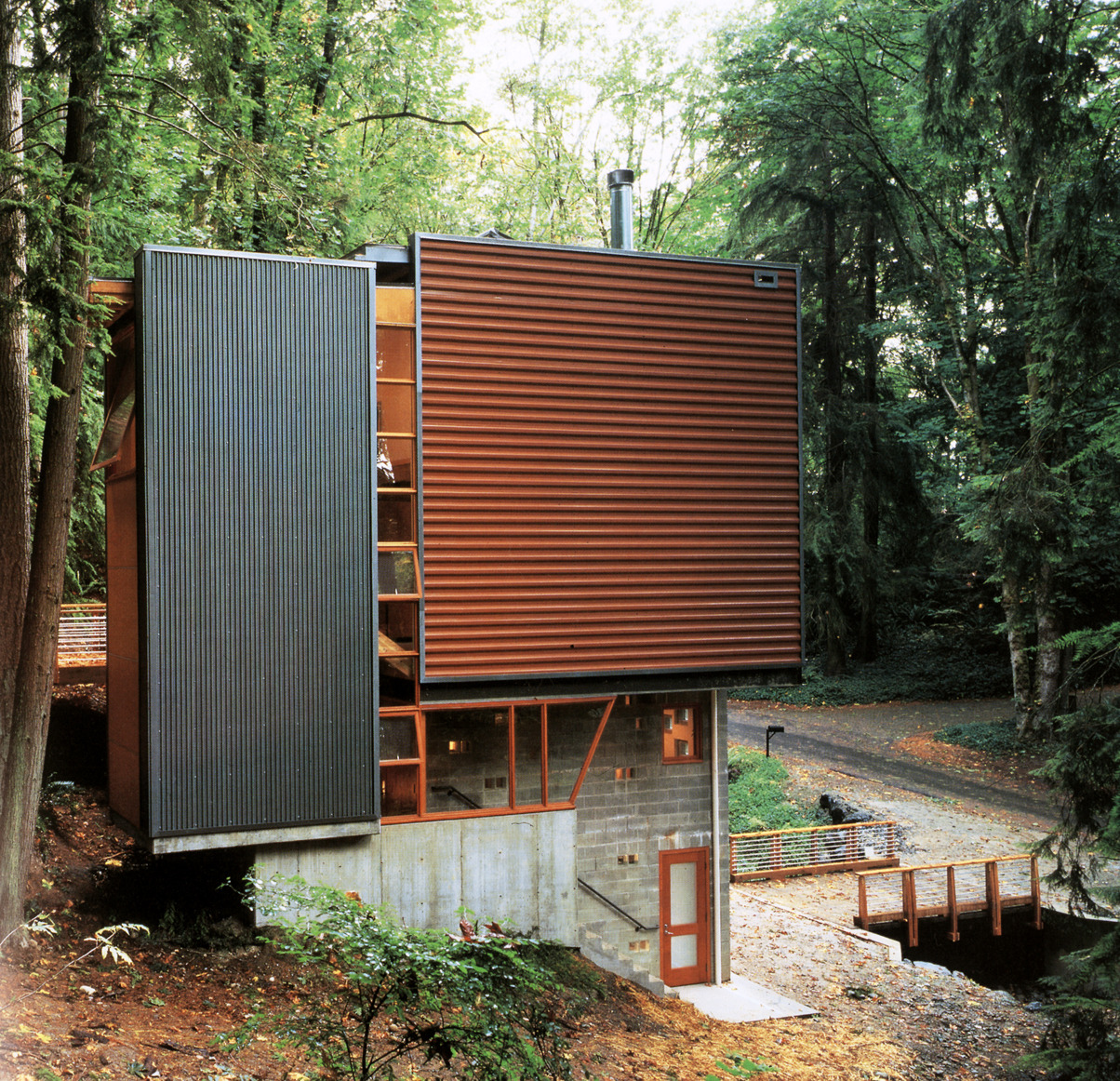
Miller Hull Architects, Michaels/Sisson Residence, Mercer Island Washington, 1998
Keep it simple.
Restraint is the common theme in the most elegant examples of architects leveraging cost effective metal siding. Simple, thoughtful details keep costs low. To keep it from looking cheap, combine these tips with thoughtful compositions which avoid complicated and expensive accessories, transitions, and penetrations.
The facade of the Michaels/Sisson House by Miller Hull is a classic example of this, but by no means the first. Decades before, the work of Glenn Murcutt was instrumental in elevating low cost metal solutions to architectural status, you can see more about some of his key projects such as the Kempsey House in New South Wales, Australia and Marie Short House in Crescent Head, Australia on the Atlas of Places.
Looking for more on metal cladding?
Check out our other resources on this topic: