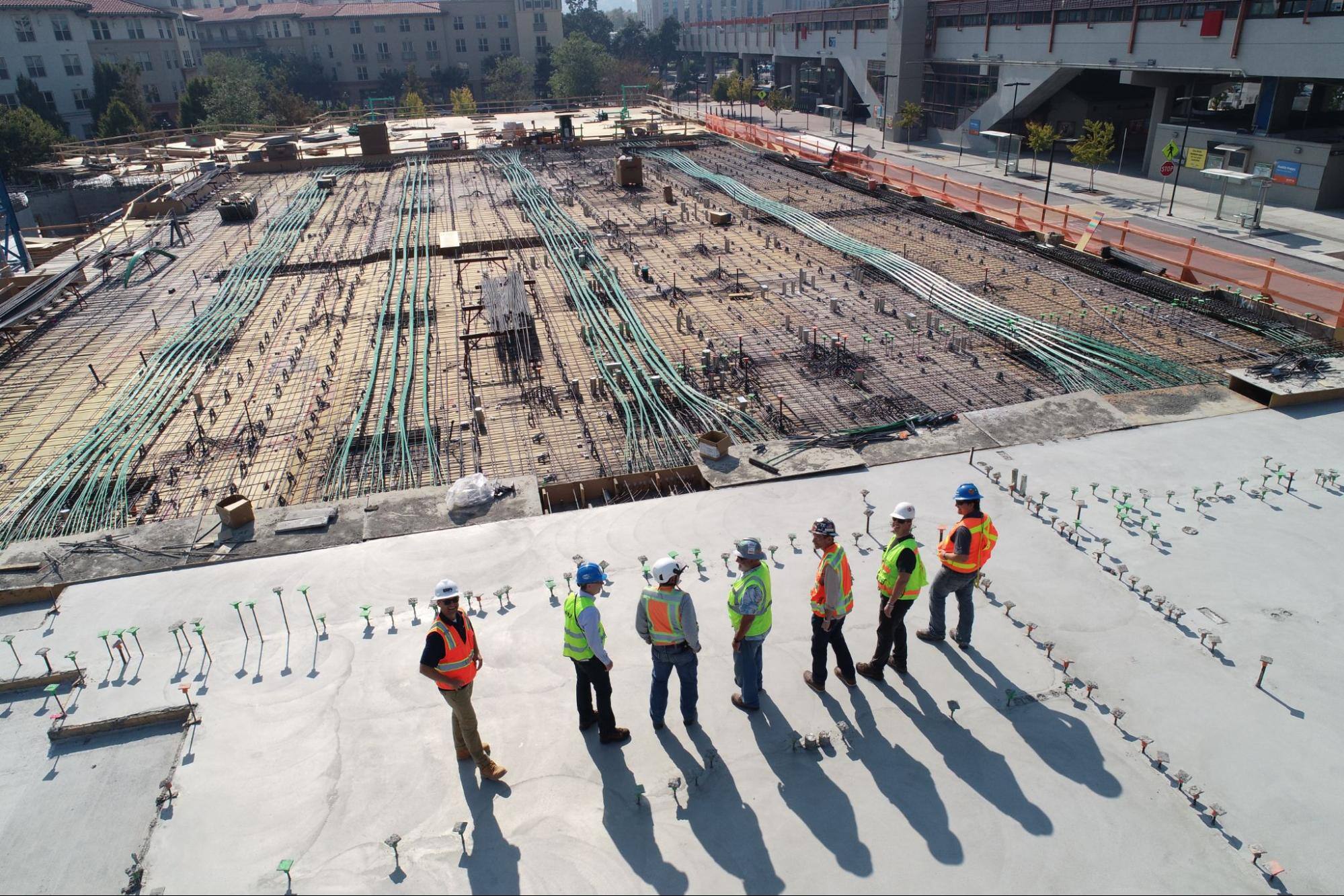
Beneath the Surface: Exploring Under-Slab Insulation Solutions
26 Sep 2023
Acelab Team
Under-slab insulation has the potential to improve a building's energy efficiency and occupant comfort significantly. By creating a thermal barrier beneath the concrete slab, it reduces heat loss in winter and heat gain in summer, which results in lower heating and cooling costs. It also helps prevent moisture infiltration, and reduces the risk of mold and other issues.
It also minimizes thermal bridging, and helps to ensure more consistent indoor temperatures and improved comfort. Overall, it contributes to a sustainable and comfortable living or working environment while offering long-term energy savings and environmental benefits.
Is Under-Slab Insulation Necessary?
The use of under-slab insulation has grown increasingly over the past several decades, and is becoming more commonly accepted as energy efficiency and building performance standards have evolved. It gained prominence in response to the energy crisis of the 1970s, with a growing awareness of the need to improve insulation in buildings.
It has since become a standard practice in many construction projects, especially in regions with extreme climates, where minimizing heat transfer through the foundation is critical for energy efficiency. The level of acceptance and implementation varies by location and building codes, but under-slab insulation is now a recognized and established practice in modern construction.
Benefits of Under-Slab Insulation
Under-slab insulation offers numerous benefits that enhance both the energy efficiency and comfort of buildings:
Energy Efficiency
By creating a thermal barrier beneath the concrete slab, it reduces heat transfer between the ground and the building's interior. This results in improved energy efficiency, with reduced heating and cooling loads, that leads to lower utility bills and a smaller carbon footprint.
Cost Savings
Lower energy consumption translates to cost savings over the lifespan of a building. The initial investment in under-slab insulation often pays for itself through reduced heating and cooling expenses.
Thermal Comfort
Insulated slabs help maintain consistent indoor temperatures, and can eliminate cold spots to ensure comfort year-round.
Moisture Control
Under-slab insulation acts as a barrier against moisture infiltration, to help prevent issues such as condensation and mold growth. This contributes to a healthier indoor environment.
Compliance
Many building codes and energy standards call for under-slab insulation to meet energy efficiency and thermal performance requirements.
Under-slab insulation offers a combination of economic, environmental, and comfort-related benefits. It plays a vital role in modern construction practices, that contributes to energy savings and the overall quality of the indoor environment.
Types of Under-Slab Insulation
Several types of under-slab insulation materials are commonly used in construction today. The materials vary in their properties and suitability for different applications. The most prevalent types include:
Extruded Polystyrene (XPS)
XPS foam insulation boards are a popular choice for under-slab applications. They offer high compressive strength, moisture resistance, and durability. XPS is known for its resistance to moisture absorption and is a particularly good match for areas with high groundwater levels.
Polyisocyanurate (ISO)
Polyisocyanurate foam boards provide excellent thermal insulation and are available with foil facings that act as vapor barriers. ISO insulation is known for its high R-value and fire resistance, which makes it a high-performance choice for under-slab applications.

Expanded Polystyrene (EPS)
EPS foam insulation is lightweight and cost-effective. It has good insulation properties, but it may not offer the same compressive strength as XPS or ISO. EPS is often used in less demanding under-slab applications.
Radiant Barrier Foil
Radiant barrier foil, when installed beneath the slab, can reflect radiant heat in order to reduce heat transfer from the ground. It is often used in conjunction with other insulation materials.
Reflective Bubble Insulation
Reflective bubble under-slab insulation, often referred to as "bubble foil insulation" or "reflective bubble wrap," consists of layers of low-density polyethylene (LDPE) or similar plastic material with small, enclosed air bubbles sandwiched between layers of reflective foil. It is typically used in warm or hot climates.
Choosing the right under-slab insulation depends on factors such as local climate, moisture levels, building codes and budget considerations. Proper installation and moisture management techniques are essential for maximizing the effectiveness of any under-slab insulation material.
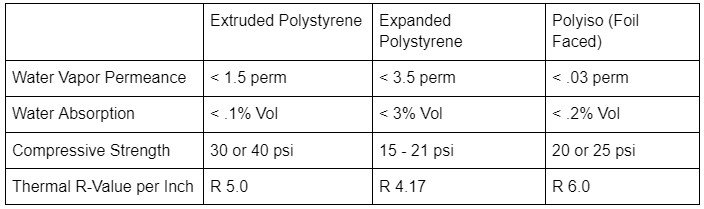
Understanding Continuous Insulation and its Relationship to Under-Slab Insulation
Integrating under-slab insulation into the building envelope as part of continuous insulation (CI) construction involves several critical steps:
Design Integration
Ensure that the design plans for under-slab insulation align with the overall CI strategy for the building. This includes determining the appropriate R-values, insulation material selection, and the placement of the under-slab insulation within the building envelope.
Seamless Transition
Create a seamless transition between the under-slab insulation and the above-grade CI components, such as wall and roof insulation. The goal is to create a continuous thermal barrier that extends throughout the entire building envelope.
Vapor Barrier
If not already an integrated element of the selected under-slab insulation, install a vapor barrier beneath the under-slab insulation to prevent moisture infiltration from the ground. The vapor barrier should extend continuously to other vapor retarders within the CI system.
Edge Insulation
Extend insulation around the perimeter of the slab, including at the slab edges and footings. This minimizes thermal bridging at the slab edges and ensures a consistent thermal envelope.
Proper Fastening
Secure the under-slab insulation in place to prevent settling or displacement over time. This may involve mechanical fasteners, adhesive, or other suitable methods depending on the insulation material.
Quality Control
Conduct inspections and quality control checks during and after installation to verify that the under-slab insulation meets specified R-values and thermal performance requirements. Ensure that seams and joints are adequately sealed.
Coordination
Collaborate with other construction trades, including concrete contractors and builders, to ensure that the under-slab insulation is properly integrated into the construction process. This coordination is essential to avoid damage during concrete pouring or other construction activities.
Compliance
Ensure that the installation complies with local building codes, energy efficiency standards, and any specific requirements related to CI and under-slab insulation.
Documentation
Maintain detailed records and documentation of the under-slab insulation installation, including material specifications, insulation thicknesses, and quality control checks.
By following these steps, under-slab insulation can be effectively integrated into the building envelope as part of a CI system. This integration enhances energy efficiency, minimizes thermal bridging, and contributes to a well-insulated and comfortable indoor environment.
Cost Considerations
The cost of under-slab insulation varies depending on the type of insulation material used. Below is a comparison of the costs of some of the most commonly used types in the U.S.:
Extruded Polystyrene (XPS)
XPS insulation boards are known for their high R-value, moisture resistance, and durability. This is also one of the more expensive options with costs ranging $0.60 to $1.20 per square foot.
Polyisocyanurate (ISO)
Polyisocyanurate insulation offers excellent thermal performance and fire resistance. The price is similar to XPS, with costs ranging from $0.60 to $1.20 per square foot.
Expanded Polystyrene (EPS)
EPS insulation is cost-effective and lightweight, but may have a slightly lower R-value compared to XPS and ISO. The cost ranges from $0.30 to $0.70 per square foot.
Reflective Bubble Insulation
Reflective bubble insulation is a more budget-friendly option. It is relatively inexpensive, with costs ranging from $0.20 to $0.50 per square foot. However, its thermal performance may be lower than rigid foam insulation.
Keep in mind that these cost ranges can vary based on factors such as location, supplier, insulation thickness, and specific product brands. While XPS and ISO are more costly upfront, they often offer higher R-values and better long-term performance, which can potentially lead to energy savings over time. Budget considerations, climate, and project goals should all be taken into consideration when choosing an under-slab insulation material.
Find the Best Under Slab Insulation Solutions with Acelab
Acelab is a cloud-based collaboration platform that offers a range of tools and resources to help architecture professionals research, compare and select building products for their projects. With Acelab, users can access product data, technical specifications, and CAD details from leading manufacturers, as well as tools to create and manage project libraries, product lists, and specification documents.
Acelab is designed to help architecture professionals save time and streamline their workflows by providing a centralized source of information and tools for building product research and specification tasks.